新素材の加工条件最適化技術
- HOME
- 新素材の加工条件最適化技術
当社の強み 4つのオンリーワン技術
導電性セラミック複合材料は基本構造が絶縁体であることから、放電加工時の最適極間位置制御が難しく、高精度対応が困難とされていましたが、様々な新素材の特性に応じた高速・高精度化技術を確立することに成功いたしました。
硬脆性材料ゆえ割れや欠けが生じやすく、まだ多くの課題を有しておりますが、反り、歪みが出にくい材料ですので、更なる「薄肉化」ニーズに応えられる最適材料の選定と、「高度化・高付加価値化」という顧客メリットの提供をめざし、新素材の微細加工による新たな価値の創出に向けて、ご一緒させていただければと願っております。
セラミックスへの高品位高精度 放電加工技術【世界初】
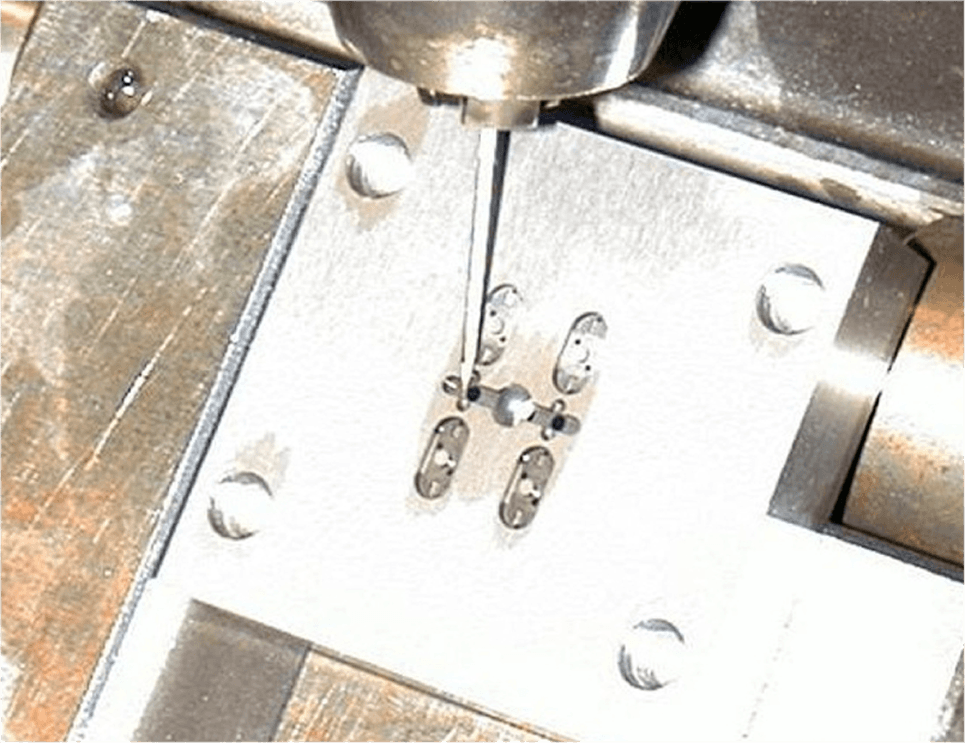
導電性セラミックスへ任意の三次元複雑微細形状の彫り込みを高速・高品位・高精度に追加工可能な革新的放電加工技術の開発に成功いたしました。
酸化物系(ジルコニア系、アルミナ系、他)、ホウ化物系、炭化物系、窒化系など、多くの導電性セラミックスの中から素材メーカー各社様との連携により、お客様の多様なニーズや様々な用途に合わせた素材選定から対応可能です。
金属からセラミックスに切り替えることによって高速高品位高精度化への対応力が飛躍的に向上し、高付加価値化をもたらします。
ジルコニア系の導電性セラミックスによる実用事例
- 金型寸法:t5×32×50mm
- Φ6.66×Φ5.50×Φ1.60×深さ0.8~1.8mm
- 携帯電話 内部機構部品8ヶ取り樹脂金型
- 下記に示すセラミックスの特長を如何なく発揮し、海外の量産工場で10倍以上のショット数に達しても腐食もなく、当初の優れた離形性を維持し続けることが可能です。
面粗度0.4μmRa
寸法精度±5μm
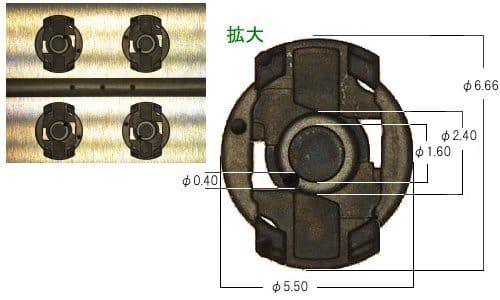
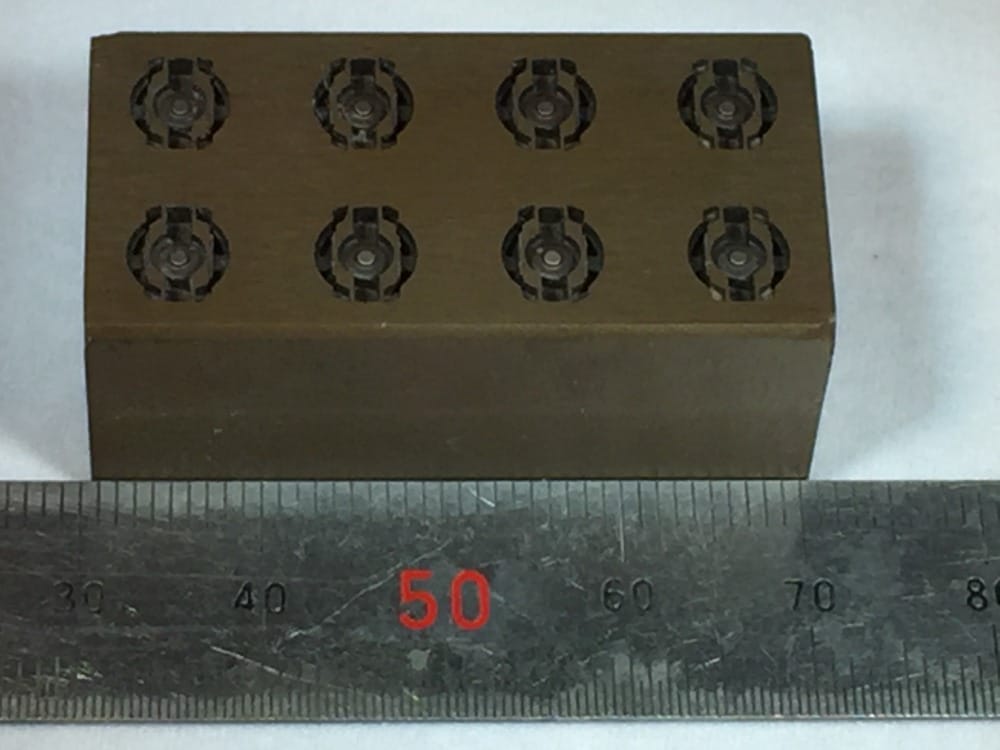
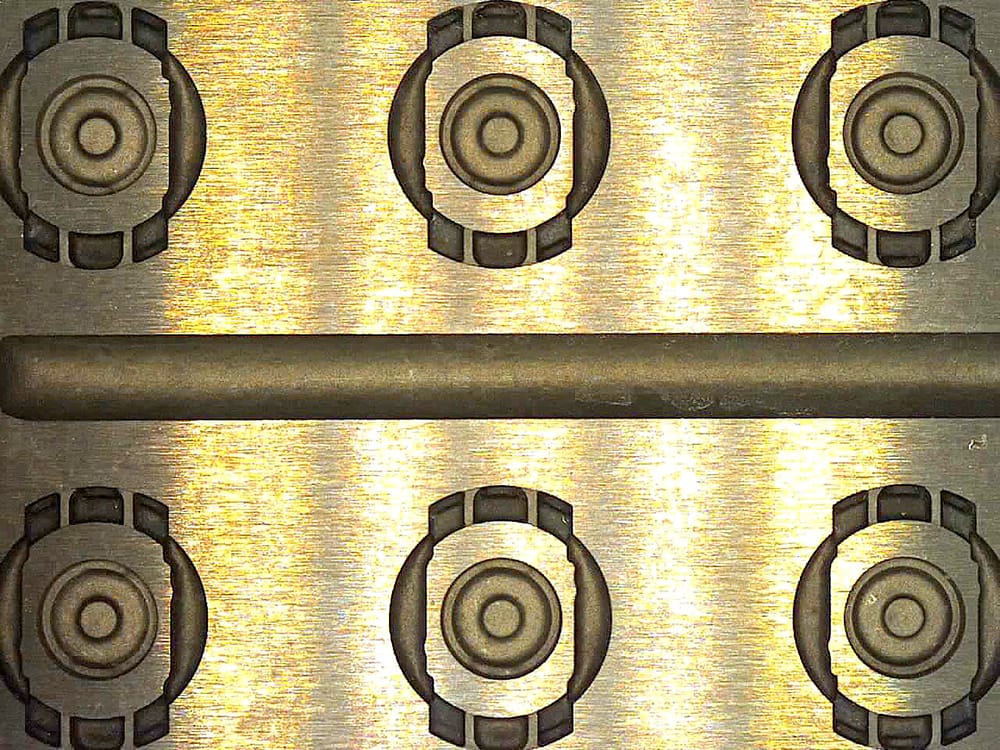
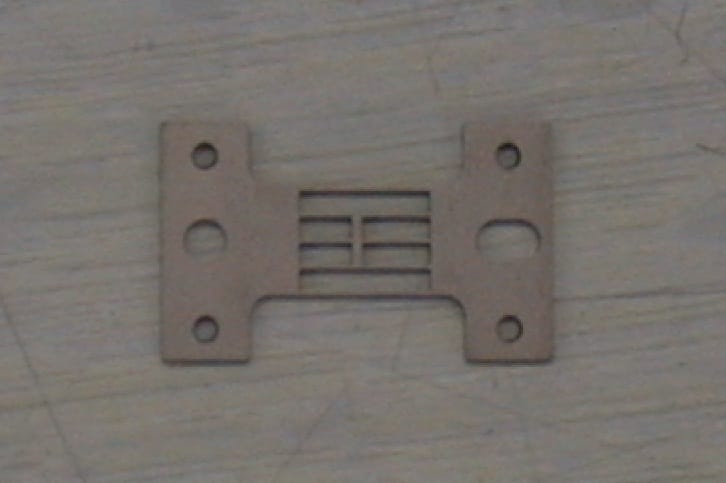
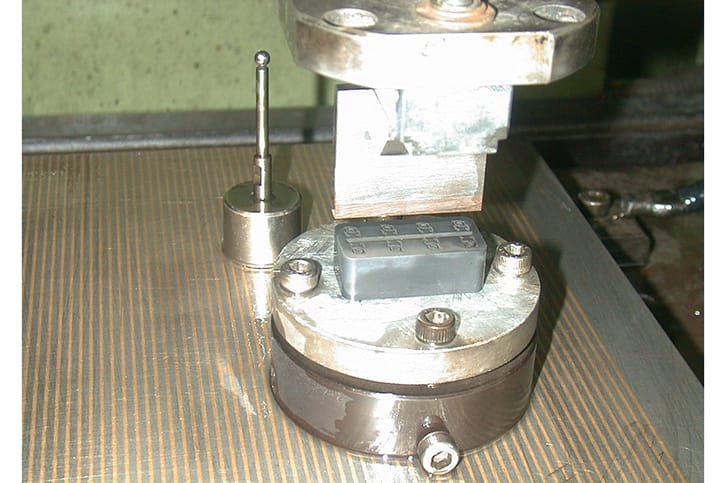
セラミックスの特徴
- 離型性がいい…摩擦係数はSKDの1/11、超硬合金の1/6
- 軽い…比重はSKDの1/2、超硬合金の1/3~1/4
- 硬い…硬度はSKDの2~5倍、超硬合金の1~2倍
- 熱変位が少ない…熱膨張係数はSKDの1/2~1/5、超硬合金の1~1/3
- 耐食性が高い…過酷な温度環境下でも長期間に亘って品質・精度の保持が可能
- 脆さが改善中…平均粒径がミクロンからナノサイズなり、割れにくくなっています
- 長寿命化が図れる…金型寿命はSKDの10~20倍、超硬合金の2~4倍
ナノテクノロジーの進化により、新素材開発は急ピッチで進んでおり、セラミックスの特性は今後ますます良くなっていきます。
現在、実用性評価のための試作依頼を随時受け付けております。なんなりとご相談ください。
セラミックスへの放電加工による精密加工部品製造のご依頼なら
精密加工部品製造のご依頼なら、セラミックスへの彫り込みを高速・高品位・高精度に追加工可能な放電加工技術を開発した当社にお任せください。