2024/10/25
精密加工領域から超精密加工領域へと進化が進むワイヤカット放電加工法
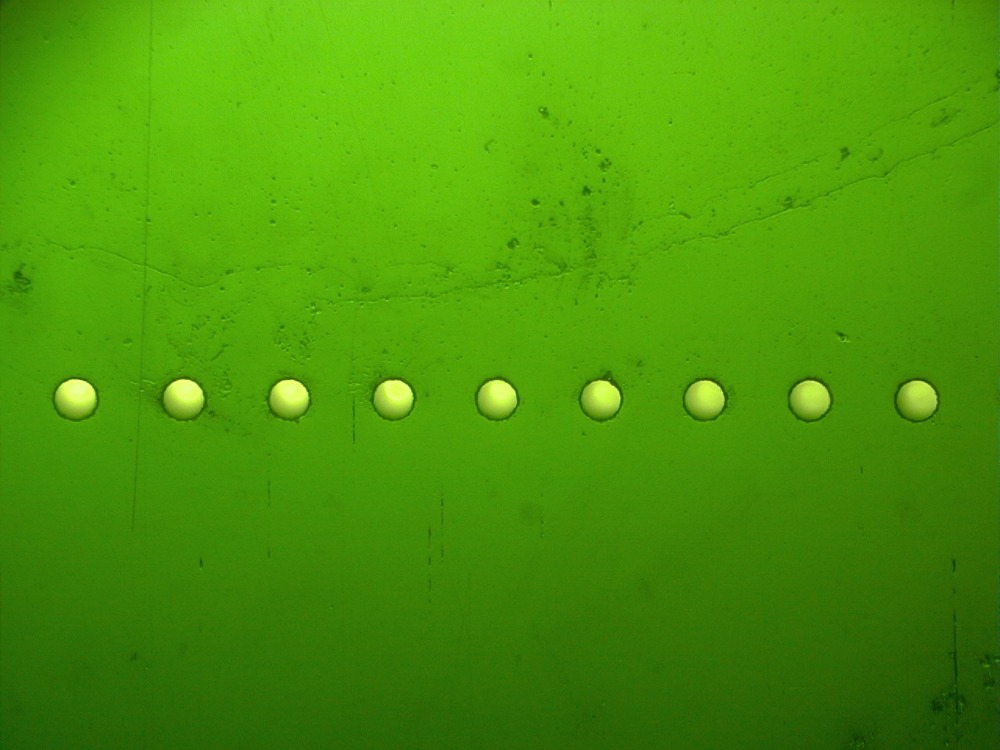
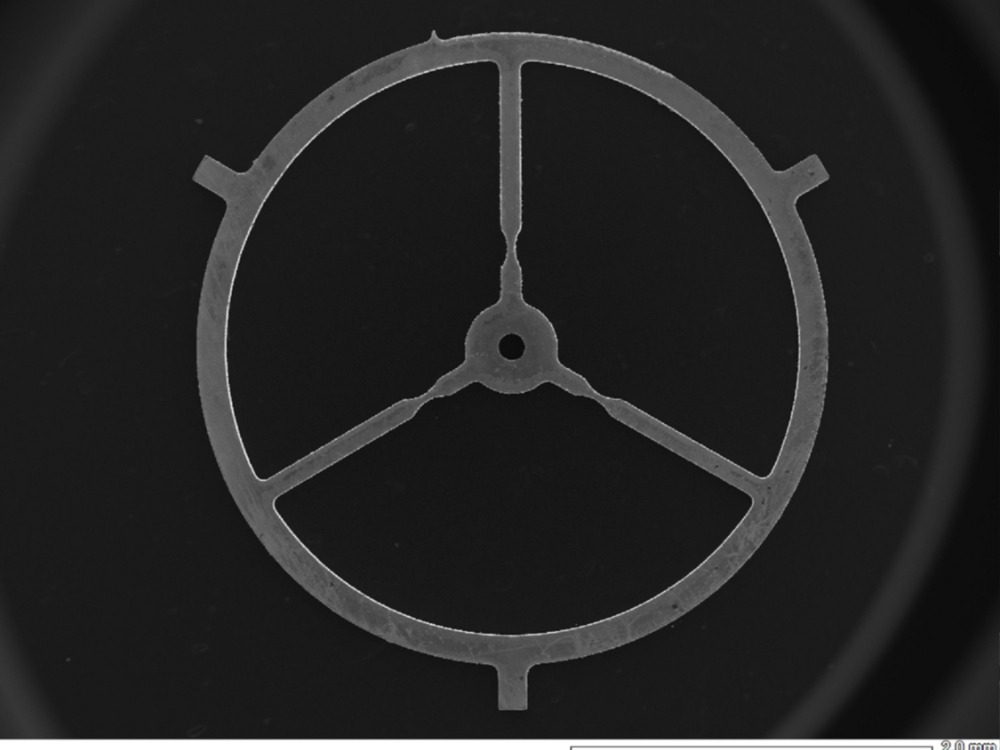
精密加工技術は、現代の製造業において重要な役割を果たしています。特に、ワイヤカット放電加工法は、高精度な部品製造において欠かせない技術です。この方法を用いることで、複雑な形状や高い精度が求められる部品を効率的に製造することが可能です。特に、金属や導電性材料の加工においてその効果が発揮され、精密加工の限界を広げています。また、超精密加工とは、ナノメートル単位の精度が求められる加工技術であり、航空機や半導体産業など、高度な基準が必要とされる分野での応用が期待されています。ワイヤカット放電加工法は、その高い精度と柔軟性から、精密加工と超精密加工の両分野において今後ますます注目されるでしょう。
精密加工とは?その定義と概念を詳しく解説
精密加工とは、ミクロン単位での高精度な加工を実現する技術を指します。その定義には、特にサイズの小さい部品や複雑な形状を扱うことが含まれています。この加工技術は、特定の製品要件を満たすために、非常に厳しい公差が適用されることが一般的です。精密加工が優れている点は、その加工精度であり、特に金属部品の製造や医療機器の製造においては、製品の性能や信頼性が直接影響を受けるため、その質が極めて重要です。さらに、精密加工は、需要が増している分野での競争力を高めるための鍵となっており、製造現場での効率を向上させるためには不可欠な技術です。このため、精密加工の理解とその利用は、製造技術者にとって重要なテーマとなります。
精密加工の具体例とその用途
精密加工は、多岐にわたる分野で利用されており、その具体的な例としては電子機器、医療機器、自動車部品などが挙げられます。精密な部品が要求されるこれらの業界では、製品の性能や精度が安全性や効率に直結するため、加工技術の確立が求められています。例えば、医療機器では、手術用器具や植え込みデバイスなど、極めて高い精度が要求される部品が数多く存在します。このように、それぞれの業界ごとに求められる精密加工のニーズが異なるため、技術者は業界特有の要件や基準を理解し、適切な加工方法を選択する必要があります。精密加工の進化は、各業界に革新をもたらし、技術の発展を支える基盤となっています。
自動車業界における精密加工の例
自動車業界では、エンジン部品やトランスミッション、ブレーキシステムなどの重要なコンポーネントが精密加工によって製造されています。特にエンジンのシリンダーやバルブなど、高い耐久性と精度が求められる部品は、非常に厳しい公差で加工されています。これにより、燃費の向上や排出ガスの削減が実現され、環境への配慮も図られています。また、自動車の小型化や軽量化が進む中で、より複雑な形状の部品が要求され、精密加工技術の発展が重要となります。高精度な加工が実現されることで、安全性を確保しつつ、走行性能を向上させることが可能となっています。
IT業界における精密加工の例
IT業界では、特に半導体製造における精密加工が非常に重要な役割を果たしています。半導体部品は、ミクロン単位の精度が必要であり、微細な回路を形成する際に高い加工技術が求められます。このため、露光やエッチングなどのプロセスが用いられ、非常にデリケートな取り扱いが必要です。また、スマートフォンやコンピュータの内部部品、さらにはデータセンターのサーバー関連機器なども、精密加工によって実現されています。高性能な電子機器が求められる現代において、IT業界は精密加工技術の進化に大きく依存しています。
航空機業界における精密加工の例
航空機業界においては、機体やエンジン部品に関して高い精度が求められます。特にエンジンは、燃焼効率や安全性に直結する重要な部分であり、その性能が航空機全体の信頼性に影響を与えます。従って、精密加工が不可欠となり、数値制御技術が活用されています。また、軽量化の観点からも複雑な形状の部品が必要であり、これに対応するために新しい加工技術が導入されています。このような精密加工は、航空機の運航における安全性を高めるだけでなく、燃費や環境への配慮にも寄与しています。
精密加工と超精密加工の進化
精密加工技術は、近年の製造業においてますます重要な役割を果たしています。製品の小型化や複雑化が進む中、精度の高い部品の需要が増加しているからです。この流れの中で、精密加工技術は進化し、より厳しい基準に適合することが求められています。特に、超精密加工という分野が注目されており、ナノメートル単位での精度が必要とされる製品が増えています。例えば、半導体や医療機器の製造においては、究極の精度が求められるため、精密加工と超精密加工の技術が連携して使用されることもあります。このような進化を遂げた加工技術は、製造の質や効率を大きく向上させる基盤です。
精密加工の精度と目指すべき基準
精密さは、製品の性能を決定づける重要な要素です。精密加工における目指すべき基準は、主に公差という形で示されます。公差は、製品の寸法や形状に対して、どれだけの誤差が許容されるかを示すものであり、精度が要求されるほど、その数値は厳しく設定されます。このような基準の達成には、高度な技術と厳密な管理が不可欠です。例えば、工作機械のメンテナンスや定期的なキャリブレーションが精密さを保つための重要な要素です。また、もちろん、素材の選定や加工条件の最適化も、精度を向上させるためには欠かせない要素となります。
超精密加工の精度とその必要性
超精密加工は、通常の精密加工に比べてさらに厳しい精度が要求されるプロセスです。特に、ナノメートル単位の精度が必要な場合、非常に高い加工技術が求められます。この精度が求められる理由としては、電子機器や医療機器の部品が非常に小型化し、かつ高度な機能を有するためです。例えば、半導体の製造工程では、数ナノメートルのズレが製品不良につながることがあります。そのため、超精密加工の技術が進化し続けることが不可欠です。これにより、製品の信頼性や性能向上を果たし、業界全体の競争力を高めることが期待されています。
超精密加工を支える環境条件と設備
超精密加工を実施するためには、生産環境や設備が特に重要な役割を果たします。工場内の温度や湿度の管理は、部品の精度に直接影響を与えるため、細心の注意が必要です。また、清浄度も加工結果を左右する重要な要因であり、微細な埃や汚れが材料に付着することを防ぐ対策が求められます。専用のクリーンルームや、振動を抑えることができる支柱や台座などの設備を導入することが重要です。加えて、高度な技術を持つ工作機械や測定機器の使用は、超精密加工の品質を確保するためには欠かせません。このような環境条件や設備の整備が、超精密加工の成功に寄与します。
主な加工技術の種類
精密加工技術には、さまざまな種類が存在し、それぞれ特有の利点や用途があります。各種加工技術は、対象とする材料や求められる精度、形状に応じて適切に選択されることが重要です。例えば、金属や樹脂、セラミックスなどの素材に対して異なる加工方法が適用され、柔軟な対応が可能となります。近年では、マイクロ加工やナノ加工といった高精度な技術も発展し、要求される精密さが高まっています。このような進展により、製造業の中で競争力を維持するために、新しい加工技術の導入が不可欠となっています。
レーザー加工の概要と特長
レーザー加工は、レーザー光を用いて材料を高温で局所的に加熱し、精度よく切断や彫刻を行う技術です。この方法は、非常に高い精度が求められる場面で役立ちます。切断ぼりの幅が狭く、変形を最小限に抑えられるため、複雑な形状の加工にも適しています。また、材料に対して直接接触することがないため、加工面が微細で美しい仕上がりになる点も魅力の一つです。さらに、レーザー加工は金属だけでなく、プラスチックや木材など、さまざまな材料に対応できるため、用途が広がります。この技術は、自動車や電子機器の部品製造をはじめとした多くの業界で活用されています。
ホーニング加工の概要と応用
ホーニング加工は、内面研削の一つであり、特に精密加工技術において重宝されています。主にシリンダーや軸など、内面の精度を高めるために用いられます。この技術は、砥石を内面に押し当てながら回転させることによって、材料を精密に削り取ります。精度の高い穴や内面の仕上げが可能で、特に高い直円度や光沢が求められる用途で効果を発揮します。自動車エンジンの部品や油圧シリンダーなど、様々な分野で使用され、耐久性を支える重要な工程として位置付けられています。精密加工技術におけるホーニング加工は、より高い性能を求める製品に不可欠なプロセスです。
放電加工の仕組みとメリット
放電加工は、電極とワークの間に放電現象を利用して金属を削り取る精密加工技術です。この方法は、硬い材料や複雑な形状を持つ部品の製造に特に有効です。放電加工においては、ワークが加工液に浸されるため、熱変形が少なく、非常に高い精度が得られることが大きなメリットとされます。また、超精密加工の領域にも対応可能で、ナノメートルの精度を要求される部品製造において注目されています。特に、モールド金型や精密部品の製造においては欠かせない技術であり、今後もその重要性が高まると考えられています。
プラズマ加工の技術と活用分野
プラズマ加工は、工業用プラズマを利用して材料の切断や溶接を行う技術です。プラズマは、高エネルギー状態の気体であり、導電性のあるあらゆる素材に対応可能です。この加工方法は、主に金属の厚物切断においてその効果を発揮し、特に工業用の大型部品や構造物の製造で重宝されています。また、精密加工技術としての側面も持ち、多様な形状に対応可能で、曲線や複雑な切断が求められる分野でも活用されています。プラズマ加工は、製造コストを削減しつつ、高品質な仕上がりを実現可能なため、多くの産業で幅広く利用されています。
溶射加工の特徴とその利点
溶射加工は、材料を溶融または半溶融の状態で対象物の表面に塗布する表面処理技術です。この技術は、耐摩耗性や耐腐食性を高めるために用いられます。溶射加工の特徴としては、対象物の温度を高く保たずに加工が行えるため、基材への熱影響が少ない点が挙げられます。様々な材料を使用できるため、アプリケーションの幅が広いことも魅力です。例えば、航空機部品や自動車部品の保護膜として利用され、長寿命化と性能向上に寄与します。近年では、エコロジーの観点からも、持続可能な材料を使用する加工方法として注目されています。
金属加工における重要なポイント
金属加工においては、精密加工技術が不可欠な要素となっています。この技術により、金属部品の形状や寸法精度を厳密に管理することが可能です。高精度が求められる現代の製造業において、製品の性能や信頼性を確保するためには、正確な加工が必要とされます。また、金属加工には様々な手法があり、各手法が持つ特性を十分に理解して選択することが重要です。適切な加工技術を選ぶことで、材料の特性を最大限に引き出し、最終製品の品質を高めることができます。このため、製造技術者は金属の性質や加工方法について深い知識を持つことが求められています。
金属材料の特性とその選定
金属加工を行う際には、使用する金属材料の特性を理解することが非常に重要です。各金属には、強度、延性、熱伝導性、腐食抵抗性など、さまざまな物理的および化学的特性があります。これらの特性が最終製品の性能に大きな影響を及ぼすため、適切な選定が求められます。例えば、鉄は強度が高く、機械部品に広く使用されていますが、腐食しやすいため、環境に応じた表面処理が必要です。一方、アルミニウムは軽量で耐食性が良好なため、航空機や自動車の部品に適しています。このように、金属の選定は、使用目的や条件に基づいて行うことが金属加工の成功に繋がります。
チタン加工の特質と応用例
チタンは、その優れた強度対比と軽量性から、金属加工において注目されています。特に航空機や医療機器、海洋産業など、厳しい性能基準が求められる分野で多く使用される素材です。チタン加工には、切削や成形、溶接などが含まれ、これらの加工方法は、チタン特有の特性に配慮して行う必要があります。たとえば、チタンは熱伝導性が低く、加工中の熱が集中しやすいため、冷却材の効果的な使用が必要です。また、チタンの耐食性は非常に高く、長寿命な部品を提供します。航空機の構造部材や医療器具などへの応用例が豊富で、ますます多くの業界での利用が進むと予想されます。
SUS加工の概要と注意点
SUS(ステンレス鋼)は、耐食性に優れた金属材料であり、精密加工技術の中でも重要な位置を占めています。特に、医療器具や食品製造設備など、衛生面が重視される分野で多く用いられることが特徴です。SUS加工においては、その耐食性を維持するために、適切な加工方法を選定することが必要です。また、加工中に生じる熱や応力によって、材料の特性が変化することもありますので、加工条件や工具選びに細心の注意を払う必要があります。さらに、SUS特有の加工硬化に対する理解も重要で、高精度が求められる部品の製造においては、経験と技術が条件となります。
精密加工に不可欠な測定と品質管理
精密加工において、測定と品質管理は非常に重要な役割を果たしています。このプロセスでは、最終製品が設計通りの仕様を満たしているかを確認するため、正確な測定が求められます。特に、高い精度が要求される部品を製造する際には、微細な寸法の変化が製品性能に大きな影響を与えるため、定期的なチェックが必要です。また、測定機器の正確さや校正状態も品質評価においては欠かせない要素です。適正な測定と管理が行われていない場合、製品不良が発生し、予期しないコストや納期の遅延を招く恐れがあります。したがって、精密加工を成功に導くためには、測定と品質管理の強化が不可欠です。
精密測定の手法とその重要性
精密測定には、様々な手法が存在し、それぞれの特性に応じて使い分けられています。例えば、三次元測定機や光学測定器具を使用することで、非常に高い精度の測定が可能です。これにより、部品の寸法や形状の確認、さらには表面粗さの評価まで行えます。精密さが求められる製品の製造では、これらの測定技術が品質を確保するための鍵となります。正確な測定値は、製品の信頼性を高めるだけでなく、製造工程の改善や無駄の低減にも寄与します。精密測定を適切に行い、結果を分析することが、現代の製造業において競争力を維持するために重要です。
加工精度の維持と公差管理
加工精度の維持と公差管理は、精密加工において忘れてはならない要素です。精度とは、製品が設計通りの寸法や形状であることを意味し、公差はその誤差範囲を示します。製造過程で生じるわずかな変動が、最終製品に重大な影響を与えることがあるため、厳密な公差設定が求められます。公差を正しく管理することで、製品の一貫性と信頼性が確保され、顧客からの信頼も向上します。また、加工の過程で定期的な測定を実施し、公差に対する適合性を確認することで、不良品の発生を防ぐことができます。このように、精密加工における公差管理は、最終製品の品質を確保するため不可欠な工程であると言えるでしょう。
室温管理の必要性と対策
室温は、精密加工において重要な環境要因の一つです。金属や他の材料は温度変化により寸法が変わるため、室温による影響を軽減することが求められます。特に、精密加工を行う際には、作業場の温度が安定していることが、部品の寸法精度を確保する上で不可欠です。温度の変動がある環境では、加工後の部品が想定通りの精度を保てないことが存在します。そのため、エアコンディショニングや温度センサーを用いた環境管理が必要になります。適切な室温管理を行うことで、製品の品質を高め、加工不良を減少させることが可能になるため、製造業ではこの対策に注力する必要があります。
工作機械と工場環境の整備
工作機械の性能や精度は、製造プロセスの効率や最終製品の品質に直結しています。適切に整備された工作機械は、安定した加工精度を維持し、高い生産能力を実現します。また、工場全体の環境整備も不可欠であり、これにより作業者の生産性や安全が向上します。温度や湿度の管理、清浄な作業環境の確保は、金属加工や部品製造において特に重要です。こうした環境が整った工場では、不具合の発生を最小限に抑えることができ、効率の良い生産体制が築かれます。したがって、工作機械の管理と工場環境の整備は、製造業における成功の鍵と言えます。
工作機械の精度向上とメンテナンス
工作機械の精度向上には、定期的なメンテナンスが欠かせません。適切なメンテナンスを実施することで、機械の性能を維持し、加工精度を向上させることができます。メンテナンス内容としては、潤滑油の補充や部品の点検、摩耗した部品の交換が挙げられます。これらの作業は、少しの時間で行える場合も多く、その効果は長期的な生産効率に大きく影響します。さらに、高精度の測定器具を使用して機械の状態を常にチェックすることで、問題が悪化する前に対応が可能になります。日頃から精密な加工を行うためには、各種の工作機械の管理を徹底し、必要なメンテナンスを行うことが重要です。
工場環境の整備と安全管理
工場環境の整備は、労働者の安全や健康を守るために不可欠です。特に、機械の使用時に発生する音や振動、または化学物質の取り扱いなど、工場内でのリスク管理は非常に重要です。具体的には、作業場所の清掃、適切な照明の設置、十分な通気性の確保などが求められます。このような環境整備により、労働者が安心して作業に集中できる環境が整います。また、定期的な安全教育や危機管理訓練を行うことで、従業員が安全意識を高め、事故の防止につながる効果も期待できます。工場全体の安全と効率を向上させるためには、徹底的な環境整備と安全管理が肝心です。
最新の技術導入とスタッフ教育
最新の技術を導入することは、競争力を維持するために重要な戦略の一つです。新しい加工技術や機械の導入によって、生産効率が向上し、より高精度な部品が製造可能となります。しかし、技術の導入だけでは不十分で、実際に操作する人による理解と技術の習得が必要です。そのため、定期的なスタッフ教育が不可欠です。新しい技術の使い方やメンテナンス方法を学ばせることにより、機械の性能を最大限に引き出すことができます。このように、最新の技術を駆使するためには、それを扱う人の技術力向上が必須となるため、両者のバランスを大切にする必要があります。
製造業における精密加工の多様な応用
製造業では、精密加工技術がさまざまな分野で重要な役割を果たしています。製造プロセスの中で、精密な部品や製品が求められる場面が多いため、この技術が不可欠と言えます。電子機器、自動車、航空機、医療機器など、多様な製品においてその需要が高まっています。特に、自動車業界ではエンジン部品やトランスミッションなど、細部にわたる高精度な加工が要求されます。また、決して無視できないのが、半導体製造分野におけるナノレベルの精密加工です。このように、各業界でのニーズに応じた精密加工は、製品の品質向上や信頼性の確保に寄与しています。
加工サービスの選び方と依頼方法
精密加工のサービスを選ぶ際には、いくつかの重要なポイントを考慮する専業者が多くいます。まず、サービス提供者の専門性を確認することが大切です。業界に特化した知識や経験を持つ企業は、要求される品質基準をクリアできる可能性が高まります。次に、過去の実績をチェックして、信頼できる業者を選ぶことが求められます。また、加工機械や設備の充実度も重要な要素です。その際、見積もりを通じてコストや納期の明確さを確認することも大切になります。依頼方法としては、希望する仕様や納期を具体的に伝えることが、良好なコミュニケーションにつながり、スムーズな進行を促すでしょう。これらのポイントを踏まえることで、最適な加工サービスを見つけることができるはずです。
精密加工の未来展望と進化の方向性
精密加工技術の進化は、今後も製造業に革新をもたらす重要な要素となります。特に、自動化やAIの導入が進む中で、精度や効率がさらに向上することが期待されます。例えば、高度なセンサー技術によるリアルタイムなデータ収集と解析は、加工過程の最適化に役立ちます。これにより、即時に問題を特定し、すばやく対応できる環境が整うでしょう。また、3Dプリンティングなどの新技術により、複雑な形状の製品を短時間で製造できる可能性も広がっています。さらに、持続可能性への配慮も重要なトレンドとなっており、環境に優しい材料やエネルギー効率の高い加工方法が求められます。このように、精密加工技術の未来は、進化と変化を通じて新たな挑戦と機会を提供し続けることでしょう。
研磨の技術とその重要性
研磨は、特に精密加工において重要なプロセスであり、表面の仕上げや寸法精度の向上を目指しています。この技術を用いることで、部品や製品の表面粗さを低減し、滑らかな仕上がりを実現することができます。研磨が持つ役割は多岐にわたり、金属、プラスチック、セラミックスなど様々な素材に適用可能です。また、研磨を行うことで部品の耐久性や機能性が向上し、最終製品の品質全体に貢献します。特に、精密部品の製造においては、研磨技術が不可欠であるため、製造業における重要な要素として位置づけられています。
研磨技術の基本とその種類
研磨には多くの種類が存在し、それぞれ異なる目的や方法で使用されます。基本的な研磨技術としては、平面研磨、外径研磨、内径研磨などがあり、各技術は特定の形状や表面状態の要求に対応することができます。また、使用される研磨材によってもその特性が大きく変わります。たとえば、ダイヤモンドやアルミナなどの研磨剤は、高い研磨精度を必要とする場合に適しています。さらに、研磨方法には機械的研磨と化学的研磨があり、用途に応じて適切な手法を選択することが重要です。これらの研磨技術は、製品の最終的な仕上がりに直接関わるため、慎重に選ぶ必要があります。
精密研磨とその用途
精密研磨は、高い精度と仕上がりを求められる場面での応用が多く見られます。特に、航空機や自動車、医療機器など、品質基準が厳しい産業で主に使用されています。これらの製品では、寸法公差や表面粗さの厳しい規定が設けられることが一般的であり、精密研磨の役割は特に重要です。また、精密研磨は、摩擦を減少させる機能を持つため、機械部品の寿命を延ばし、性能を向上させる効果も期待されます。具体的には、ギアやシャフト、ベアリングなどの部品に応用され、それらはすべて精密研磨からの恩恵を受けています。このことから、精密研磨は製造業においてなくてはならない技術といえるでしょう。
研磨の測定と品質保証対策
研磨のプロセスでは、仕上がりに対する測定と品質保証が欠かせません。具体的には、研磨後の表面粗さを測定することで、製品が求める仕様を満たしているかを確認します。この測定には、接触式の測定器や非接触式の測定器が使用され、精度を確保するための基準に従っています。また、研磨プロセス中にも、リアルタイムでのモニタリングが求められるため、機械の調整や加工条件の変更を適宜行う必要があります。さらに、定期的な品質検査を実施し、不良品の発生を未然に防ぐための対策が重要です。これにより、研磨工程の品質を維持し、最終製品の品質保証につなげることが可能となります。